Page 1 of 2
BLADE CRACK THEORY
Posted: Tue May 03, 2011 3:18 pm
by 9121u
I think blade crack is caused by misalignment of the inner to the outer.because the manual says to align using rivet on trailing edge.witch should be OK to do but.i found on some of these brantlys the rivets are not true in line or the rivets are out of misalignment..and if this is not checked first the outer blades are going to be off...if i remember right there was a old service letter on installing caps on the trailing of the inner blades because of tin canning an some was probably don in the field so it did not get done properly....so i think the outer to the inner blades should be aligned with a laser pointer.from a better point of reference.not the old string method.that's old school way...it was OK back in the day..and i think if your blades are back from being straight the have a tendency to pull there self straight and only way it can do that is to pull on blade dampers and when the bottom out then it starts pulling on blade skin and that means cracking will occur this also take out the dampeners.and if the blades are to far forward its going to pucker the blades by the rivets also....so this is my opinion.....i would like LYLE TO COMENT ON THIS.... THERE HAS TO BE A GOOD REASON THESE BLADES ARE CRACKING.......THANKS TOM 9121u
Re: BLADE CRACK THEORY
Posted: Wed May 04, 2011 5:44 am
by bryancobb
My 2 cents.
Every cracked blade has the same failure scenario. The cracks follow the row of rivets that curve around the root rib, progressing rearward to the AN-3 bolt at the lag damper. This area of the skin is obviously the weak or weakened link in the chain.
By design, the blades are constantly leading/lagging in flight. The amount of lead/lag varies with the severity of the maneuvering the pilot does.
Now...the blade is a long lever-arm that has a lot of force to act on the dampers, the root rib, AND THE THIN 0.018" thick skin. Every rivet hole that is punched in the skin, eats away at the collective tensile strength of the aluminum skin in the vicinity where cracking occurs.
In addition to the dampener compressing/stretching, the skinny tapered shape of the weak root rib flexes when the blade leads/lags. This, in my opinion, is what starts the skin cracking.
The root rib, again in my opinion, needs to be more rigid for the cracking to not occur. Imagine a drawn line from the center of the AN-3 damper bolt, at 45 degrees toward the front d-spar to the center of the nearest skin-to-spar rivet. THIS measurement MUST NOT be changing in flight as the long blade leads/lags and acts on the root rib. The damper must be the ONLY thing that gives.
IN MY OPINION, AS DESIGNED, THE ROOT RIB GETS TOO THIN AS IT TAPERS REARWARD AND ACTUALLY IS NOT RIGID ENOUGH TO MAKE THE DAMPER DO ALL OF THE FLEXING.
This is obviously a problem area with ALL helicopter blades. If you look, a large percentage of blades have layered skins in the root area that are several layers of doublers, progressively getting smaller as they near the lead/lag hinge or drag-link.
I had considered experimenting on my ship several years ago, with putting two 1/16" thick by 1/2" wide straps on the top and bottom. The root end of the straps would be fastened by the AN-3 damper bolt. The front end of the straps would be fastened to the spar by removing ONE skin rivet, and replacing it with an NAS62XX/95-KSI bolt. This would practically eliminate any flexing in the root rib and force the damper to do its' job This contraption could be easily bolted onto an existing blade and the only modification would be removing ONE rivet at the spar/skin joint, which could be replaced if the experiment didn't work.
I never got around to oing it before I dsold my ship??
Re: BLADE CRACK THEORY
Posted: Sun May 08, 2011 7:50 am
by HELISCAN
Bryan;
Do you know how difficult it would be to get FAA approval to reskin the blades? Not for me (of course), but for a certified shop. Lots of shops are out there for all types of aircraft parts on the secondary market. I'll bet Lance at Cartersville could get certified, that guy can do anything, (with your help).
Dave
Re: BLADE CRACK THEORY
Posted: Sun May 08, 2011 3:52 pm
by bryancobb
Hey Dave,
How are y'all. I hope Patsy is back 10-8 / 10-41 LOL!
It can be done (getting pma'd to reskin the blades). It would be a costly setup and certification process. There's a fella here at VPC who got an STC to build a fold out motor mount and install a FRANKLIN 6 CYLINDER on a customer's Cessna 180 or 185 ? I saw his books and papers and photos and flight test data.
It looked like he had spent 1000 +/- hours of legwork plus a couple hundred flight hours! That's probably a similar endeavor. Getting someone "SOLD" on going this route would be a big obstacle. I'm quite sure Lance could learn to do this and since he is already a repair center, I think it could qualify as a REPAIR, since the original spars and hinge blocks are used.
Learning to be successful at the process (I failed at my first try) and getting the flight-testing out of the way, and geting the process certified would probably be a full-time job for almost a year, for 1 person.
Just doesn't sound good does it?
Re: BLADE CRACK THEORY
Posted: Mon May 09, 2011 6:39 am
by HELISCAN
Bryan;
Patsy is doing just great, thanks for asking. Back almost 100%. For those who do not know, my wife had a liver transplant Nov. 1st, 2009, "on her birthday".
Back to the blade issue, I knew you would know how to do it. Sounds like the investment in time may not be cost effective unless Lance had a number of pre-orders with a nice down payment. That could get his attention. The question would be, what would they cost? My guess is that he could easily compete with Harolds $3,000 for used blades. In fact, I'll bet Harold would be his first customer, I think he has about a dozon blades that need repairs.
Dave
Re: BLADE CRACK THEORY
Posted: Mon May 09, 2011 9:46 am
by bryancobb
After getting proficient at it, two guys could repair one blade in 3 days. One day for disassembly, removing old rivets, cleanup, inspection, and priming surfaces that will be inside with zinc chromate,
one day for adhering the skin and foam and curing the adhesive in the heat box, and the last day for installing 150+ double-bucked rivets to spec.
EACH blade MUST have the foam/skin extend a couple of inches beyond the tip so a sample can be cut off and destructive-tested for aluminum to foam bond strength. This becomes part of the permanent record for THAT BLADE.
Then foam can be removed at the tip, for the aluminum tip rib to be bonded and riveted in place.
For those who have never seen the inside of a 202 blade, here's a quick sketch I drew.
Some of my thoughts:
1) Possibly 0.020" thick bonded skin doubler in triangular area from spar rivet #10 to damper bolt to spar rivet #1. ??? ( see drawing )
2) A higher-tech modern adhesive that is more appropriate and doesn't require heat-cure. ??
3) Off-The-Shelf, less custom dampers that can be had for less than $300 each. ??
4) Using numerous clamps instead of vacuum bagging during adhesive curing stage. ??
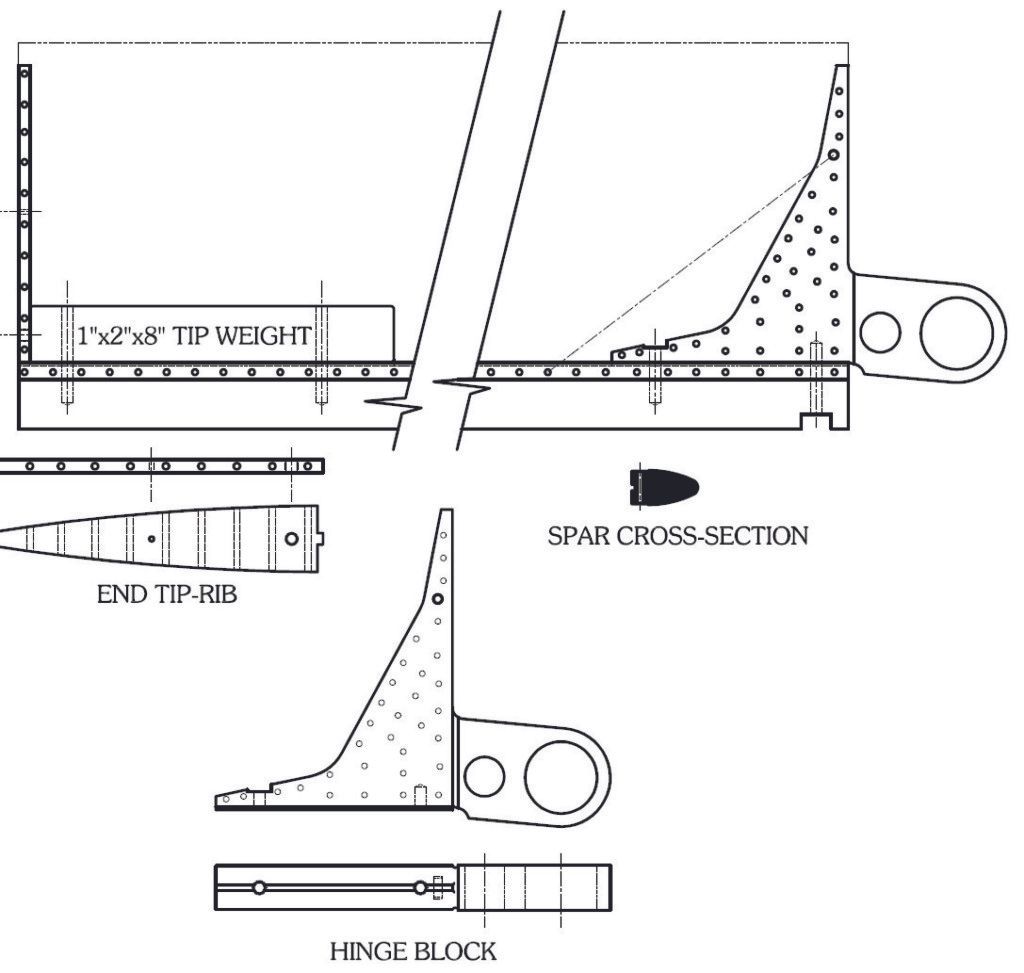
Re: BLADE CRACK THEORY
Posted: Mon May 09, 2011 1:30 pm
by HELISCAN
OK let's see how many blade orders are needed. Although not yet tested, I think mine are OK for now, but to be safe I would order one.
By the way Bryan, what is different about the 404's. Are they under the same SB?
Dave
Re: BLADE CRACK THEORY
Posted: Mon May 09, 2011 1:37 pm
by bryancobb
HELISCAN wrote:OK let's see how many blade orders are needed. Although not yet tested, I think mine are OK for now, but to be safe I would order one.
By the way Bryan, what is different about the 404's. Are they under the same SB?
Dave
Doyle and I discussed it once, and I don't remember ANY differences for sure. I do remember that he said the FAA required them to update the procedure for the production certificate to be awarded, and it SEEMS like the original foam manufacturer was out of business and the new foam had a little difference. It's been 10 years and I just can't remember all the facts.
Here's the MFG of the adhesive. It is a pint kit of B2TAN.
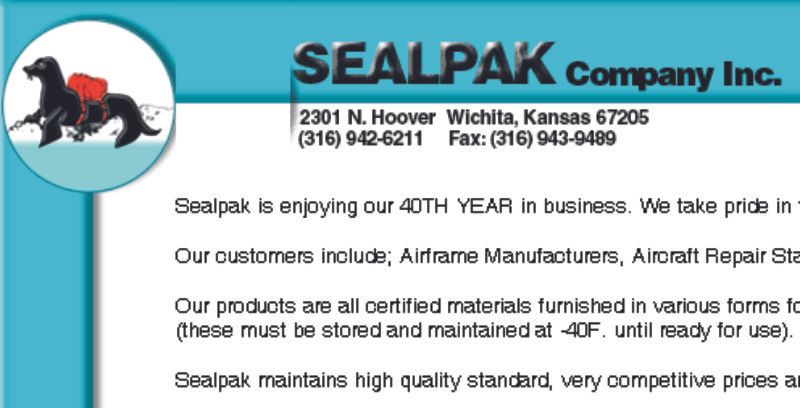
Re: BLADE CRACK THEORY
Posted: Mon May 09, 2011 1:40 pm
by seneca2e
Very nice job on the drawing and the concept seems imminently sensible with the doubler. Whether there would be some issue involved with stiffening that area with a doubler that we can't think of I don't know. It seems clear that if that area was restrained from flexing that the skin would not crack.
The B2B fleet did go thru a tremendous amount of hard training hours during the Brantly-Hynes factory school days. It seems if the design were truly inadequate they'd have been cracking out the ying yang during that era. Improvements can always be made and certainly your idea seems logical to me.
Re: BLADE CRACK THEORY
Posted: Mon May 09, 2011 2:16 pm
by seneca2e
Different foam and glue due to availability issues are the only differences noted between 404 and 202 blades according to factory personel I spoke to a couple of years ago.
Re: BLADE CRACK THEORY
Posted: Tue May 10, 2011 8:18 am
by bryancobb
Did anyone notice that (2) AN-4 bolts, in shear, is all that holds the hinge block to the spar!!!
Those two bolts and the friction they create at the faying surfaces of the spar and hinge block,
carries ALL the centrifugal load of the outer blade!!!!
They are 160,000 PSI tensile strength and 95,000 PSI shear strength, but It looks skimpy!
Re: BLADE CRACK THEORY
Posted: Tue Jan 31, 2012 11:38 pm
by Mike Victor
It is not often I respond to the dialogue here, but I see comments based on lack of historical experience, it compells me to encourage contributors to explore the history of this machine. These machines were used in a dozen or so very active flight schools during its first dozen years or so; and the factory flight school was extremely active in the 1970's... there have only been a few active flight schools in the past decade where they were flown over 200 hours per month.
In the higher utilization environments, the items mentioned today were addressed. The cracks in the skins got attention with details to root causes and corrective processes. Causal factors included elements not mentioned on this forum. In addition, at least one FAA certified Repair Station developed approved process specifications for reskinning, repairing and overhauling blades... and yes, any of these procedures on a rotor blade is a major repair; and requires approved data, approved processes, and a quality system for return to service. These historical models were well developed with criteria for various levels of repairs and/or reskinning, foam, weights, ribs, and hinge blocks. There were many with the expertise who did reskin and repair these blades for quite a few years with FAA Approved methods and materials.
In my opinion, those asserting that the loss of a PC in some way forfeits a type certificate holders intellectual property rights, is the sort of thing that leads to nightmares. The production certificate (PC) is required to produce aircraft and issuing airworthiness certificates by the company...
In the alternative method, there have been many limited production aircraft, including Brantly's which were built one at a time without a production certificate, by the type certificate holder or a licensee of the TC holder; where the FAA then must do the conformity inspection and issue an airworthiness certificate.
Trying to use TC Holder drawings accessed without the written authorization in the rule; would not be good... especially where so many engage in dialogue about their quests. It could be handled as theft of intellectual property or the Federal Laws for TC and STC's, or the FAA falsification statutes. The penalties are severe and do not promote an ability to engage in aviation for the long haul.
Few appreciate these little machines more than I do; and we all should thank Harold for trying to do his best to keep them going durnig some tough times. I believe he was working on a B2B right to the end... as was his passion. He will be missed.
I believe we need to have some patience, and solicit a cooperative attitude about licensing from the TC holder; to enable development or reinstatement of the repair process specifications as approved long ago. Maybe there could be a win win which would help Brantly International and the US owners.
Re: BLADE CRACK THEORY
Posted: Wed Feb 01, 2012 5:48 pm
by 9121u
HI Mike good to see you on the forum. THE way i see it on some of these parts especially the blades.is to do all the research I don't think it would be not worth it. because of the few that's out there flying ? say you get blades going.that's fine now what abought clutch/ bearing shafts some of that low time components.those parts might not be available. to get made then one could wast money if you could not get some of the other parts....I don't no just guessing on this matter.right now I have a very good low time b2b. now the question to my self... is.. do I sell or keep flying it till its junk.then donate it to a museum.have been thinking abought this for a wile now.because there is not a good affordable and safe helicopter out there..like the brantly....what do you guys think...tom
Re: BLADE CRACK THEORY
Posted: Wed Feb 29, 2012 11:58 am
by G-ATLO
The UK importer (BEAS) of Brantlys inthe 60s and 70s had drawings done and certified by the CAA to put a doubler on the Blade root.They did this because of the amount of Blades being fast started by students.I have sourced the CAA ref but they cannot find the Approved drawings.I know someone in the UK has them as I have heard rumours of a modified blade (not used any more)in existence .I will keep searching,it only took me ten years to find the jump leads that fit!
Re: BLADE CRACK THEORY
Posted: Sat Apr 21, 2012 7:24 pm
by N2285U
Can someone please update the status of the assemblies that are currently critical to keeping the B2B AOG?
Did SB111 ever become an AD? Are new blades available if so? With the passing of Harold and many of the blades cracking I am sure good (legal) used blades are tough to find. I never did like the way the dampner mounted to the blade as well. It seems that these blades either cracked or the hole where the dampner bolt went through would oblong. I realize that the fitting of the blade to the dampner may have been the problem there.
What about the FormSprag unit? My last ship had the -3 (I think) version and I still could not figure out what it's true retirement time was.
Finally, is the tail rotor still a concern?
I owned 2 B2Bs in the past and really liked them. I'm thinking about a helicopter again and the B2B is on my short list.
Thanks